Retro-Coat Protects Residents at Site of Former NYC Industrial Warehouse
Project snapshot highlights:
- Preemptive solution mitigates potential vapor intrusion threat in New York City
- Retro-Coat provides building residents assurance they are safe from breathing any potential contaminants from prior site uses
- Retro-Coat’s custom finish adds visual appeal to the interior space, enhancing the residents’ living environment
A former 20,000-square-foot industrial warehouse in the Bronx has been transformed into a residence for the community’s housing-insecure population. Based on the property’s history and the surrounding land use, the presence of contaminants such as petroleum hydrocarbons and chlorinated solvents could not be ruled out. Consequently, the developers worked with the City to develop a preemptive solution to mitigate the potential chemical vapor intrusion (VI) concern. Retro-Coat® — a vapor intrusion mitigation system designed as a long-term solution for protecting indoor air in existing buildings — was proposed.
Retro-Coat Protects Los Angeles Contemporary Art Gallery
Case study highlights:
- Retro-Coat Vapor Intrusion Coating System application achieved compliance with the Los Angeles Regional Water Quality Control Board (LARWQCB) standards for VI mitigation
- Retro-Coat chosen as a low-cost mitigation solution with outstanding chemical resistance that provides aesthetic value to a building’s interior space
- Land Science Certified Applicator, Systems Waterproofing ensured the manufacturer’s specifications were strictly followed
This case study reviews a site where PCE (perchloroethene) was detected in the soil gas beneath a commercial building housing a contemporary art gallery and studio suite in a Los Angeles neighborhood. A Vapor Intrusion Mitigation Plan using Retro-Coat from Land Science was quickly reviewed and approved by LARWQCB.
Proven Strategies for Protection Against Vapor Intrusion in Existing Buildings
In this webinar we were pleased to have special guest speaker Tracy Fajette, Business Development Manager at American Industrial Coatings join us. His presentation discussed the application of Retro-Coat Vapor Intrusion Coating technology from Land Science. Nick Mjolsness, West Region Manager at Land Science, joined him and discussed how Retro-Coat technology effectively mitigates contaminant vapor intrusion risk for existing buildings.
Learn the following in this free webinar:
- How Retro-Coat mitigates vapor intrusion risks
- Which contaminants Retro-Coat protects against
- Technical processes involved in the installation of Retro-Coat
- Case studies demonstrating how application challenges can be overcome
Recording now available
Complete the form below to view this free webinar.
A Growing Manufacturing Company Brings New Jobs to Lansing Area following Retro-Coat Treatment
Project snapshot highlights:
- Retro-Coat Allows Repurposed Industrial Building to Create Jobs in Michigan Community
- 140,000 Square Feet Manufacturing Facility Successfully Treated
A growing manufacturer looking to expand its operations purchased a vacant industrial facility in Lansing, Michigan, where chlorinated solvents were used and spilled into the subsurface. The environmental consultant was asked to address the suspected vapor intrusion concerns resulting from the former industrial operations. In working with the Michigan Department of Environment, Great Lakes & Energy (EGLE), the consultant proposed utilizing the Retro-Coat® Vapor Intrusion Coating System, in combination with passive venting, to ensure safe indoor air for the future workers. EGLE approved the vapor mitigation approach to address the potential indoor air concerns. The Retro-Coat installation was sequentially phased in accordance to the construction schedule, where the Certified Applicator worked closely with the general contractor and the consultant to meet project expectations and deadlines. Since the Retro-Coat system will act as the wearing surface at this facility, the Retro-Coat Top WB topcoat was also applied to maintain the desired aesthetic of the building owner. Following the Retro-Coat and passive venting system’s successful application, the potential exposure pathway has been mitigated, and the site is eligible for restricted site closure designation by EGLE.
Future Retail Tenants Can Breathe Easier Knowing That Vapors Will Not Intrude
Project snapshot highlights:
- Former Dry Cleaning Operations Transformed Into Safe Retail Storefront Property
- TerraShield with Retro-Coat Complete Remediation Efforts
- First Installation in Los Angeles County
The first TerraShield installation completed in Los Angeles County is a former dry cleaning site redeveloped to make way for a retail storefront. Chlorinated solvents and benzene were present in the subsurface left by past site activities requiring ongoing active remediation over a several year period. The Los Angeles Regional Water Quality Control Board oversaw the site remediation efforts, which included soil excavation and operation of a soil vapor extraction system to remove the majority of the contaminants. Although these efforts effectively removed most of the contamination, lower concentrations remained in the soil gas, prompting the need for a vapor mitigation solution. The environmental consultant and their client chose TerraShield® to provide the maximum protection available to protect future retail tenants from potential exposure to harmful chlorinated solvent and benzene vapors. TerraShield was installed at grade, terminating at a concrete slab in the building that remained following soil excavation activities. Retro-Coat™, a chemical-resistant surface coating effective in mitigating vapor intrusion, was also applied to the existing concrete slab and used as a finished floor surface.
Retro-Coat 101: A Complete Guide to the Retro-Coat Vapor Barrier System
Preemptive Vapor Mitigation Protects Students from Potential Exposure
Preemptive Vapor Mitigation Protects Students from Potential Exposure
This case study reviews a high school that has been a fixture in its Southern California community since it was built in the 1930’s. Due to onsite pesticide use, a vapor intrusion mitigation system was necessary to protect students and staff. The environmental team responsible for treating the potential vapor intrusion identified the historical use of pesticides on site and voluntarily sought a remedial solution to protect the site’s future occupants. In efforts to protect students and staff against potentially harmful vapor intrusion as a result of historic releases, a vapor intrusion barrier system was proposed as the most appropriate remedial approach.
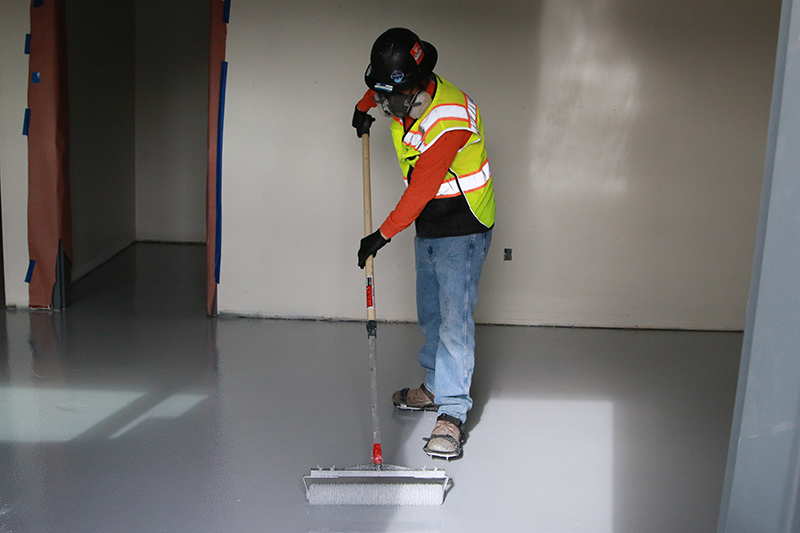
This case study features the following:
- High school is located in an urban Southern California area with more than 3,000 students.
- Due to onsite pesticide use, a vapor intrusion mitigation system was necessary to protect students and staff.
- The vapor barrier was applied throughout the 14,000 square foot library building located on-campus.
Retro-Coat Utilized to Prevent Harmful TCE and Chloroform Vapor Intrusion
A former industrial manufacturing facility in Greenville, SC was purchased for redevelopment in 2017. Building improvements were planned to include a warehouse, offices and self-storage units to serve a growing commercial area. Now located within an urban commercial land use area of Greenville, redevelopment plans included converting the industrial warehouse building into climate controlled self-storage units, and renovating the office into an apartment unit and office.
Prior to purchasing the site in 2017, the current site owners entered into a Voluntary Cleanup Contract and Brownfields agreement with the South Carolina Department of Health and Environmental Control (SCDHEC). The Brownfields agreement allowed the site owners to purchase the site while receiving SCDHEC liability protection for existing environmental contamination by agreeing to perform certain environmental assessment, mitigation, or remediation activities.

This case study features the following:
- The Retro-Coat barrier and Vapor-Vent system were incorporated into already planned renovations, saving the site owner time and money.
- Retro-Coat is resistant to both TCE and chloroform and is a wearing surface, rated for foot and forklift traffic.
- The Retro-Coat system layers cure quickly, reducing building downtime.
- The combination of Retro-Coat and Vapor-Vent was chosen as a remedial solution to mitigate the risk of harmful vapor intrusion.
Retro-Coat Applied to Former Jazz Club Ensures Protection from Vapor Intrusion
Subsurface contamination caused by chlorinated volatile organic compounds (CVOCs) beneath a former jazz club posed a direct risk to the indoor air quality for a Renton, Washington property. The CVOCs had migrated beneath the property from a neighboring dry cleaning operation resulting in a vapor intrusion (VI) issue. When environmental consultant Maul Foster Alongi performed a cost analysis of different vapor mitigation and remediation approaches, it was found that the Retro Coat™ Vapor Intrusion Coating System would provide an excellent solution at about a third of the cost less than other remedial approaches.
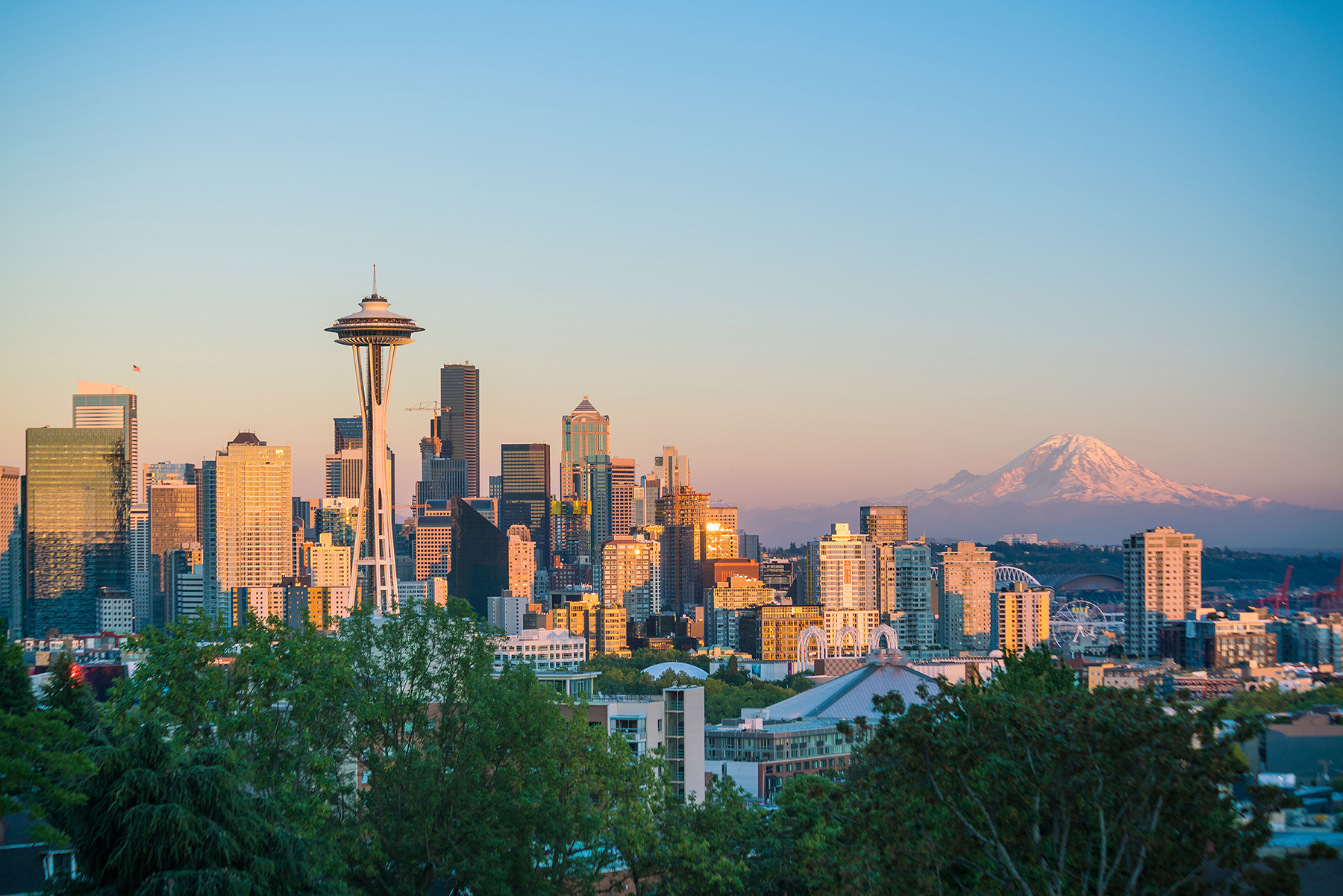
This case study features the following:
- How Maul Foster Alongi achieved 33% cost savings compared to alternative remedial approaches
- Indoor air quality evaluation of TCE and other VOCs
- Retro-Coat application details
- Vapor mitigation performance results and indoor air quality findings after the installation of Retro-Coat
Retro-Coat Helps Speed Real Estate Transaction
Project Highlights
- Retro-Coat functioned as a vapor intrusion mitigation membrane as well as a long-lasting coating for the basement level, accomplishing two of the owner’s goals with one product.
- Retro-Coat was chosen as the most feasible and effective treatment due to compatibility with pre-existing methane mitigation system components.
- Retro-Coat is resistant to harmful methane gas intrusion and is a wearing surface, meaning no additional concrete protection is necessary.
- The updated vapor intrusion mitigation system allowed for the new tenants to move in quickly.
- Retro-Coat is applied without any odor and cures quickly, reducing building downtime.
Project Summary
An office building located on the San Francisco Peninsula was left vacant for multiple years. The building is located on top of a capped landfill which is a known methane producer. After a recent change in ownership, it was important for the new owner to make the necessary improvements to the building so that new tenants could move in quickly. One of these improvements was to update the vapor mitigation system to ensure the tenant’s safety from any harmful vapor intrusion.
The owner enlisted the expertise of Langan to update the vapor mitigation system. Langan proposed using Retro-Coat Vapor Intrusion Coating System because of its proven resistance to harmful vapors and its durability. The owner was thoroughly pleased with this application because it accomplished two goals with a single product: it mitigated the harmful vapor intrusion and provided a durable coating for the floor of the basement level. Retro-Coat’s multi-functionality saved the site owner time and money.
Technology Description
Retro-Coat Vapor Intrusion Coating consists of chemically resistant materials which protect existing structures from the threat of contaminant vapor intrusion. Retro-Coat was developed by experienced vapor intrusion specialists and is proven to resist the most aggressive chemical vapors. This technology acts as a protective barrier eliminating the need to remove the existing slab and when combined with in situ treatment, it can greatly lower remediation costs.
RESULTS
Retro-Coat consists of chemically resistant materials which will protect this structure from the threat of contaminant vapor intrusion, specifically methane gas. Retro-Coat finishes to a high gloss, easy-to-clean surface that is impervious to vapor and moisture transmission. Additionally, Retro-Coat withstands foot traffic and industrial settings. It was significant to have a highly durable coating system in place because the tenants plan to use the basement level to house large computers and heavy technological equipment.
The site owner has been very pleased with the outcomes from Retro-Coat. The building’s basement level has a highly durable coating and most importantly, the vapor intrusion mitigation system is now highly effective.